STANDARDS FOR DESIGN AND INSTALLATION OF INDUSTRIAL LPG SYSTEMS TCVN 7441: 2004
29/10/2024
*Note: This is a content regulated by the Law, so it may include specialized terminology, and the content will be long and detailed.
Currently, there are many national standards applied to LPG such as: TCVN 6152:1996, TCVN 7221:2002, TCVN 6486:2008, but specifically for industrial LPG systems, TCVN 7441:2004 (Liquefied Petroleum Gas (LPG) Supply System at the Point of Consumption - Design, Installation and Operation Requirements) is applied.
1. On industrial LPG system design requirements
Overall requirements for industrial LPG system design according to TCVN 7441:2004 include:
- System installation location: OUTDOOR, VENTILATED to easily disperse exhaust gas/leakage.
- There must be a fence surrounding the station, the fence must still ensure VENTILATION.
- The bottom of the tank base must be flat so that LPG does not have space to accumulate.
- Regulations on industrial LPG system safety tables.
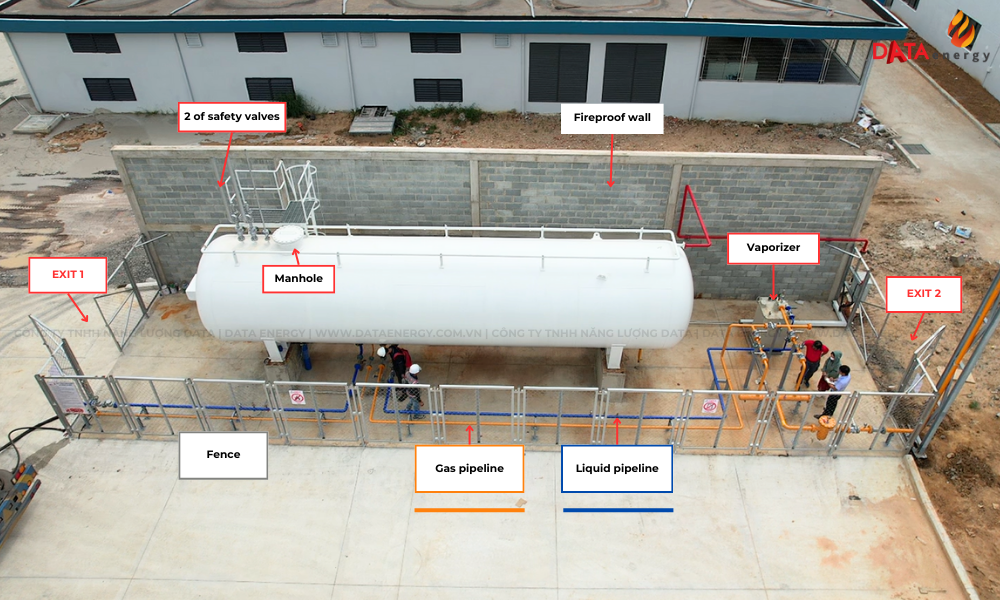
2. TCVN 7441:2004 regulations on LPG tanks
- LPG tanks must be designed, manufactured and inspected according to TCVN 6486:1999, TCVN 6153:1996, TCVN 6154:1996 and TCVN 6008:1995 standards and related requirements.
- There must be a tank information label on the tank body.
- For tanks with a capacity of less than or equal to 20,000 liters, there must be at least 1 safety valve. For tanks larger than 20,000 liters, there must be at least 2 safety valves.
- Liquid LPG filled into the tank must not exceed 90% of the tank capacity.
- Each LPG tank must be equipped with at least one level indicator mounted permanently on the tank.
- All LPG tanks must have a manhole or inspection door. In case the tank has a manhole, if it is oval, the minimum size is 400 mm x 300 mm or circular with a minimum diameter of 400 mm.
- LPG tanks must have a pressure gauge installed in the saturated LPG vapor space on top of the tank.
- The position of the tank to the station fence must be greater than or equal to 1.5m.
- Regulations on tank installation location and distance to neighboring structures
Learn about underground tanks
3. About fire walls
- When using a fire wall, the maximum separation distance can be reduced by 30% compared to the required separation distance when there is no fire wall.
- The fire wall must be built of brick or concrete, at least 0.5m higher than the height of the tank, 0.75m longer on each side and fire resistant for at least 150 minutes.
4. Vaporizers
-
The pressure-bearing parts of the vaporizer must be designed and manufactured for LPG. The machine label must clearly state the manufacturing standards, origin, manufacturer's name and serial number, date of manufacture, and vaporization capacity. The design temperature and maximum working pressure for the pressure-bearing parts of the vaporizer must meet the maximum pressure and temperature conditions during operation.
-
The vaporizer must be equipped with an appropriate automatic control valve (e.g. thermal expansion type, solenoid type or float type) to prevent liquid LPG from spilling into the space and LPG vapor pipeline.
-
The vaporizer must be installed at least 1.5m away from the tank. At least 3m away from neighboring construction.
5. TCVN 7441:2004 requirements for other equipment
All equipment and materials used for industrial LPG systems must be designed and manufactured for specialized use with LPG
- Pressure regulator: Includes level 1 pressure regulator and level 2 pressure regulator. After level 1 pressure regulator, gas pressure is usually lower than 1.4 bar. After level 2 pressure regulator, gas pressure usually depends on the burner or production machine specified.
- Pipeline system: Pipelines can be installed above ground or buried underground. Pipelines must be installed away from sources of excessive heat or cold or must have protective measures to avoid this impact.
- Pipelines must be protected from corrosion. For above ground pipes, LPG vapor pipes are painted yellow, LPG liquid pipes are painted in a color other than yellow. (Usually blue)
- Bottom drain valve: is required for LPG tanks and vaporizers.
6. TCVN 7441:2004 fire and explosion prevention requirements
Minimum number of fire extinguishers for LPG storage and vaporizer storage
7. Requirements for testing, commissioning, operation and maintenance
Tank equipment, vaporizers, valves and pipelines must be inspected by competent authorities.
After completing the installation, the pressure, leakage and welds on the entire system must be checked. Finally, the process of deflating and cleaning the LPG system with inert gas (usually nitrogen) to push all oxygen and water out.
* System test:
- Must ensure that the fire sprinkler system and fire extinguishers always operate properly.
- Technical staff set the pressure of the pressure regulator valve at the lowest level and gradually adjust it to the operating pressure during the test run.
* Operation:
Industrial LPG systems do not require specialized technical staff to operate 24/7 like CNG, but at the customer's point of consumption, there must be someone in charge and instructed on the operation of:
- Understanding the operating principles of the entire industrial LPG system.
- Filling methods and notes when filling LPG.
- Handling emergencies and using fire fighting equipment.
* Maintenance of industrial LPG systems:
TCVN 7441:2004 stipulates that the entire system must be periodically maintained no more than every 5 years.
DATA Energy is a unit that designs, installs industrial LPG systems and maintains LPG systems every 3 months. And supports troubleshooting 24/7.
See more about LPG system maintenance procedures Video here
* Regulations on technical inspection and acceptance:
If you need clarification on any of the regulations, please contact DATA Energy: 02862.757.005
More Information:
DATA ENERGY COMPANY LIMITED (DATA Energy)
- Supply LPG, CNG, LNG.
- Consult, Design, Install Industrial Gas System.
- Invest Gas System (LPG, CNG, LNG) for the factory.